Quantifying NanoPak-C All Carbon Microbeads Potential to Reduce CO2 emissions & Electricity Usuage
- MS
- Oct 20, 2024
- 5 min read
Our previous blogs have qualitatively explained how our technology and products are positively impacting sustainability. In this blog, we're taking it a step further by quantifying the potential of our products to reduce greenhouse gas (GHG) emissions.
Keeping it simple, we use acetonitrile, a widely used organic solvent in large-scale reversed-phase chromatography, as an example. It's a modifier that enhances separation efficiency. We employ a published Life cycle assessment (LCA) model [1] to demonstrate how saving acetonitrile translates into GHG reduction, measured in tons of CO2 abated and grid-generated electricity in kilowatt-hours (kWhs) reduced yearly.
Solvents are critical in making pharmaceuticals. They comprise 80–90% of the materials used in chemical
reactions and around 60% of the energy needed to produce an active pharmaceutical ingredient (API). While solvents don't take part in the chemical reactions, they provide the necessary environment for these reactions to happen. Solvents also help purify the API during steps like separation and washing. The most common way to dispose of solvent waste is through incineration.
The latest (year 2022) data from the Toxic Release Inventory (TRI) showed that the U.S. pharmaceutical industry produced 350 million kilograms of waste considered hazardous by the EPA. This amount is almost four times what was reported in 2008 [1]. The top ten solvents used in making pharmaceuticals account for over 80% of this waste, with acetonitrile being one of them. This situation underscores the urgent need to tackle issues related to solvent waste management.
Benefits of Life Cycle Assessment (LCA). Life cycle assessment (LCA) helps us understand the emissions linked to solvent production, waste disposal, and recycling in pharmaceutical manufacturing.
LCA is a method for analyzing the environmental effects of a product, process, or service from start to finish. It looks at the impact on nature from the time we gather materials until they are discarded. This thorough method prevents us from simply shifting environmental problems from one area to another.
The LCA process has four main steps:
1. Goal Definition and Scoping: Here, we define what we are assessing, set the context for the analysis, and outline the boundaries of the study.
2. Inventory Analysis: This step identifies and counts all the energy, materials, and emissions involved throughout the life cycle of the product or process.
3. Impact Assessment: In this stage, we evaluate the potential effects on people and the environment based on the inventory data.
4. Interpretation: Finally, we look at the results from the previous steps to determine which process or product is better for the environment.
The LCA process is not linear; we may revisit earlier steps and adjust our interpretations based on new findings. This method has been effectively used in several industries, including electronics, electricity production, fuel transportation, and pharmaceuticals.
LCA of acetonitrile. We used a published life cycle assessment (LCA) of acetonitrile and other common organic solvents to examine their greenhouse gas (GHG) emissions and the amount of electricity produced from the grid during their life cycle [1]. This life cycle includes their production, use in processes, and waste treatment. This study found that the biggest environmental impacts come from production and waste treatment, which are often ignored. Emissions during the use of the solvent were seen as minimal, based on the idea that no solvent is consumed during use. Also, emissions from activities like pumping, mixing, and heating are small compared to the emissions from production and waste treatment.
Table 1 presents the LCA for producing 1 kg of acetonitrile.
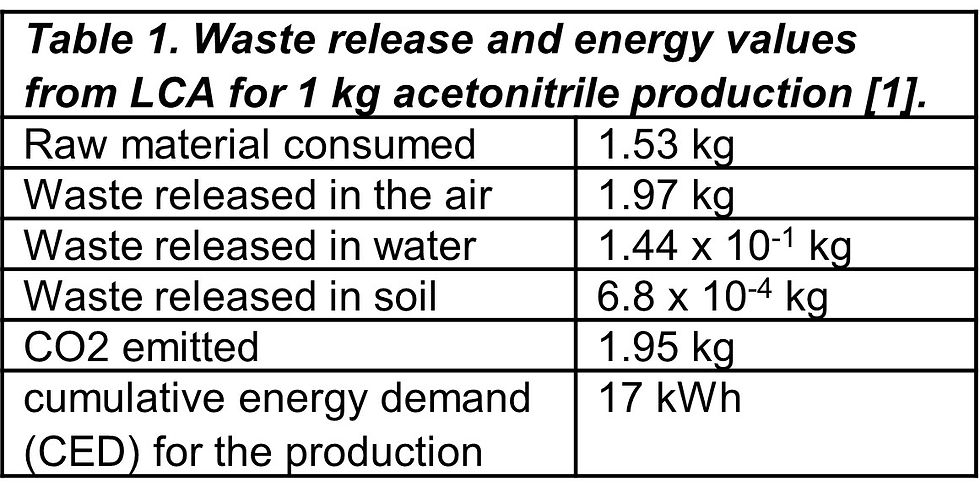
The study's results indicated that large amounts of CO2 emissions come from acquiring raw materials, producing, and transporting solvents. The carbon dioxide and greenhouse gas emissions from burning these solvents also contribute significantly to their overall emissions. Studies show that about half of the greenhouse gas emissions and 40% of energy used in the life cycle of an active pharmaceutical ingredient (API) stem from burning solvent waste [2].
Reducing the fresh solvent needed for a process can greatly lower its carbon footprint. Solvent recovery and reduction systems can help cut these emissions significantly.
Acetronitrile usage in purification and its impact of greenhouse gas (GHG) emissions. Using the purification of the peptide drug glucagon-like peptide (GLP)-1 as an example, we have estimated that to purify 1 kg of GLP-1, about 3000 kg of acetonitrile is needed. . This use leads to emissions of about 5850 kg (or 5.85 tons) of CO2, along with consuming 51,000 kWh of electricity from the grid.
Using a formula to calculate emissions, we find that the electricity consumed results in about 43,350 kg (or 43.35 tons) of CO2 emissions. This means the total CO2 emissions from purifying 1 kg of GLP-1 reach approximately 49,200 kg (or 49.2 tons).
If we need to manufacture 1 ton of these peptides each year, the CO2 emissions from acetonitrile would total about 49.2 kilotons.
To give you an idea of how significant this is, it is about 1% of the annual emissions from a typical coal-fired power plant, which emits around 4.6 megatons of CO2 each year.
Broader implications. The four main organic solvents used in solid-state peptide synthesis followed by purification, are dimethylformamide (DMF), N-Methyl-2-pyrrolidone (NMP), dichloromethane (DCM), and acetonitrile (ACN). DMF, NMP, and DCM are used during the initial stages of solid-state peptide synthesis. ACN is used later in the purification process. Together, these solvents make up more than 90% of what is used in peptide synthesis [3].
Table 2 shows the life cycle assessment (LCA) for producing 1 kg of a “generic solvent.” This “generic solvent” represents an average of the solvents studied in the LCA.

Comparing Table 1 and Table 2, we see that the order of magnitude of CO2 emissions and electricity used in making a generic solvent are similar to that of acetonitrile.
As discussed above, reducing the use of acetonitrile alone can significantly help reduce climate change. Therefore, cutting back on the use of other solvents in peptide and pharmaceutical production will also lead to a clear and substantial drop in greenhouse gas emissions.
This blog is part of our broader impact series, which provides an easy-to-understand overview of the implications of our technology and products on science, sustainability, and human health.
For more information on how our NanoPak-C All Carbon media can address your peptide purification challenges or or to request samples, please email us at inquiry@millennialscientific.com, call us at 855 388 2800, or fill in our online form.
References.
[1] M.J. Raymond, C.S. Slater, M.J. Savelski, LCA approach to the analysis of solvent waste issues in the pharmaceutical industry, Green Chemistry 12(10) (2010) 1826-1834.
[2] C. Jiménez-González, A.D. Curzons, D.J.C. Constable, V.L. Cunningham, Cradle-to-gate life cycle inventory and assessment of pharmaceutical compounds, The International Journal of Life Cycle Assessment 9(2) (2004) 114-121.
[3] I. Kekessie, K. Wegner, I. Martinez, M.E. Kopach, T.D. White, J.K. Tom, M.N. Kenworthy, F. Gallou, J. Lopez, S.G. Koenig, P.R. Payne, S. Eissler, B. Arumugam, C. Li, S. Mukherjee, A. Isidro-Llobet, O. Ludemann-Hombourger, P. Richardson, J. Kittelmann, D. Sejer Pedersen, L.J. van den Bos, Process Mass Intensity (PMI): A holistic analysis of current peptide manufacturing processes informs sustainability in peptide synthesis, The Journal of Organic Chemistry 89(7) (2024) 4261-4282.
Comments